One thing I can say is no matter how much I read over the past 6 months or how many videos I watched during this preparation period, it barely prepares you for the actual work itself once you start.
So one thing I realized this morning is that the 8 dowels in my my SCAT Volksaver 69mm Counterweighted Crankshaft do not fit into the 8 dowel holes of the generic lightened flywheel I purchased from CIP1 last October. And lo and behold, at CIP1 there is the following warning posted on the item:
SPECIAL NOTE ABOUT DOWEL PIN HOLES: These flywheels come pre-drill from the factory with the standard S.P.G. 8 dowel pin hole off-set pattern – we have had some customers call with concerns that the new flywheel does not slip onto their crankshaft dowel pins easily. Please note that it may be necessary to test fit YOUR crank to this flywheel before final assembly. A small amount of interference (or press fit) will be expected and you will need to determine if any slight reaming of the dowel pin hole will be required. If any reaming is required – this is a very easy procedure which should only take a few minutes with the correct tools. Please be patient and remember that every 8 dowelled crankshaft in the market today has been drilled by someone other then Volkswagen. Since any one of 1000’s of different shops or individuals may have drilled the dowel pins in your crankshaft- it is impossible to guarantee that ANY flywheel will slip onto the pins without some small amount of fitting.
Of course, I see this now as I’m writing this blog post and not all these past few months.
So… it looks like I’ll be having to ream the dowel holes some before final assembly.
Camshaft Assembly
I did my best to use it as a vertical stand for the crank anyway.
The con rods and there bearings when on ok, with their bumps to the top of the case and the threads sealed with Loctite and torqued to 25 ft/lbs.
The next steps proved to be a bit more of a pain in the ass. Some vids make it look so easy but it wasn’t.
The timing gear, the distributor gear, and the spacer between them all needed to be heated up enough so they would slightly slide over the crankshaft and the wood ruff key that locks them in and aligns them together.
This was repeated over and over until I finally could get them on. They did require some force as well, something that nobody in the vids I watched really had. I suppose it could be related to the amount of heat I used, but inevitably the whole thing got assembled.
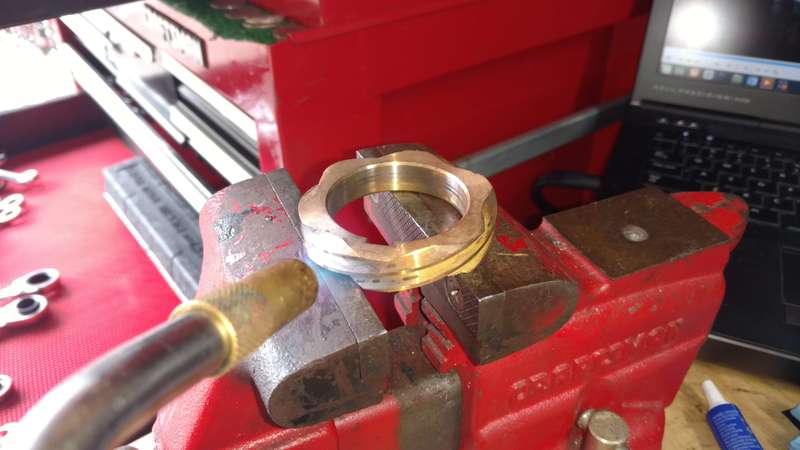
In doing all of this gear work, I ended up slicing my thumb fairly deeply and at first, I honestly didn’t notice it until I saw all this darker red and realized it wasn’t the reddish Redline Assembly Lube. There I was, bleeding all over the crank and tools.
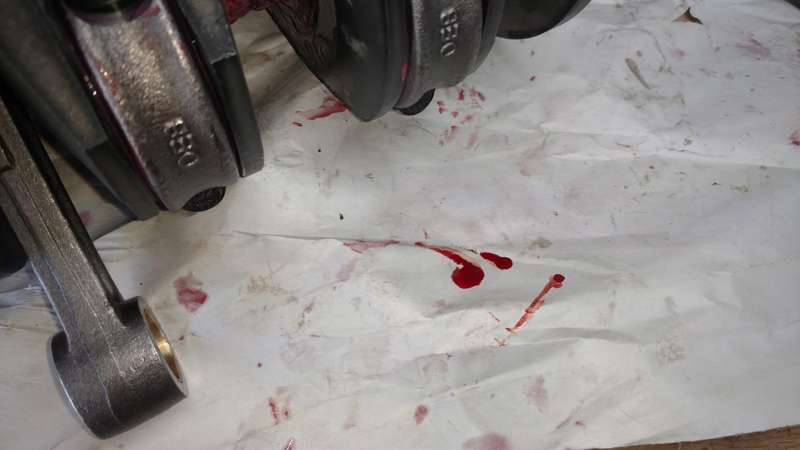
My blood and spirit is inside this engine’s “bones” now. (It had better have been worth it.)
After I cleaned up and bandaged myself I needed something easier to finish so I got on to something else.
Pressure Valves
This actually took longer than I planned as the first one (near the crank pulley end) felt like it wasn’t moving too smoothly.
I ended up lubing up the bore and forcing and old one in and out until it moved freely.
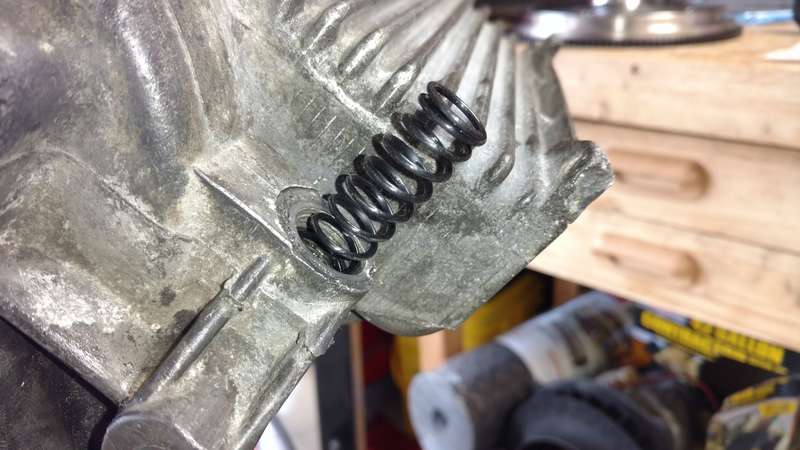
The longer spring for this bore seems so strong and too large for this but it looks about the same as the 45 year old one. I oiled it all up and using the screw with a crush washer to hold it, slowly pushed it down until I could get the threads started.

Let me say that after the nightmare of disassembling and removing the stock “flat head” style screws, the hex plug screws I bought from SoCalParts was a wise replacement. So much easier. VW should have done this 50+ years ago!
Cam Assembly
So the SCAT C20 cam kit from Summit Racing I bought of course did not come with bolts to put the gear on the cam itself. The bolts I did buy I thought should go on easy. Of course, the were not metric! So my son ran to his shop and brought me a massively expensive Snap On set of pretty much every hex and torx bolt I could want. Turned out it was a 3/16 allen. My 4.5mm would likely have stripped the hell out of them even attempting it.
I got it all assembled and torqued to 18 ft/lbs.
I really need to start thinking in newton/meters.
I so need to dedicate myself to totally converting my life to metric even though I live in 1 one of 3 countries on the entire planet that scoffs at actually finally converting to a sensible form of measures!
But I digress.
The whole measurements thing gets me angry.